3D printing turns digital models into physical objects by adding material one layer at a time. The process is also known as additive manufacturing, and it’s revolutionizing the way we make things.
Most 3D printers use a software program to specify print settings and slice the digital model into layers representing horizontal cross-sections of the object. These programs, such as Cura and PrusaSlicer, are often open-source. Click the Visit Website to learn more.
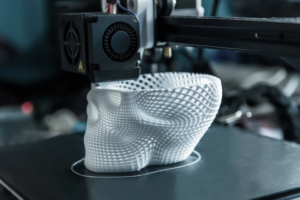
Prototyping using 3D printing technology allows for early and iterative development of product concepts. Creating prototypes at this stage saves time and money later in the process by minimizing the number of changes needed to bring a new product to market. This helps companies stay competitive in the fast-moving consumer market, which requires faster product development and technology innovation.
The use of 3D printers to create prototypes has become an essential tool in the modern manufacturing and product design industry. From mechanical components and architectural models to intricate jewelry designs, and consumer products, this innovative technology is used to test and refine products before full-scale production. This method of prototyping reduces product development cycles, saving companies money and allowing them to get their products to market faster than their competitors.
In addition to the cost savings associated with rapid prototyping, this technology also offers a high level of precision and durability compared to traditional manufacturing techniques. This can reduce the amount of material wasted during the production process, while enabling manufacturers to produce parts with greater strength and dimensional accuracy.
It is important to establish clear testing criteria and performance metrics for a given prototype. This will help ensure that the finished product meets desired specifications and expectations. It is also important to include all stakeholders in the testing and evaluation process. This will allow for better communication and decision-making, as well as a more accurate picture of the potential impact of any changes or modifications on the prototype’s functionality.
Testing a prototype’s structural integrity is also a vital part of the process. It is important to use a variety of test methods to evaluate the structure and determine any areas for improvement or reinforcement. For example, a team might consider adding internal supports to critical areas of the model to increase its overall strength and durability.
In addition to structural tests, it is important to perform a range of user tests to ensure the prototype is easy to use and understand. This can be done by conducting user interviews and observational studies to collect direct feedback on the prototype’s usability and functionality. Moreover, the team should document all testing results and feedback to facilitate further product iteration.
Rapid Manufacturing
The rapid manufacturing of functional prototypes using 3D printing technology is now a viable alternative to traditional tooling. This can save time, money and resources by eliminating the need to invest in a mould – a costly process that requires weeks to above a month and produces only one part at a time.
The first step in rapid manufacturing is creating a 3D digital model of the design using computer-aided design (CAD) software. This model can then be converted into an STL file, a format that represents the surface geometry of the object as a series of triangles that can be understood by a 3D printer. Once the file is sliced, it can be fed to a 3D printer, which will build up the model layer by layer.
A wide selection of materials can be used in 3D printing, allowing for a variety of applications. In addition to the standard plastics, metals and elastomers, the technology also offers bioprinting and other innovative materials that expand the possibilities of the technology. For example, conductive filaments and glow-in-the-dark plastics allow for the creation of unique electronics and wearable items, while a wide variety of polymers and composites enhance mechanical properties such as strength and stiffness.
Many industries are leveraging the capabilities of 3D printing for rapid prototyping and production purposes. Automakers, for instance, use the technology to test designs and tweak them with unprecedented speed, enabling more innovation and reduced time to market. Manufacturers are also leveraging the technology to produce spare parts for their products, reducing inventory and increasing efficiency.
Jewelers are also embracing the capabilities of 3D printing to create a wide range of intricate, customizable pieces. This allows them to sidestep some of the limitations of traditional jewelry making techniques, such as CNC machining and lost-wax casting.
Rapid manufacturing of functional prototypes using 3D printing can be challenging as a result of the lengthy print times and the potential for errors in the finished product. To minimize these challenges, manufacturers should ensure that they optimize their models for the 3D printing process and follow best practices when designing for 3D printing. This includes ensuring that the model is a good fit for the final design and taking into account factors such as weight, size and durability. Additionally, the printed prototype may require additional post-processing to remove support structures, sand rough edges and apply paint or other finishes.
Customization
3D printing is an additive manufacturing technology that builds a physical object layer by layer by deposition of materials directly from a computer-aided design (CAD) model. This allows for an unprecedented degree of customization in end-use products, allowing for parts to be tailored for specific users or application needs. In addition, 3D printed objects can be made more quickly and inexpensively than traditionally fabricated components, providing cost-effective solutions for low-volume production runs.
The first step in customizing a part for 3D printing is to prepare the digital model, or STL or OBJ file, using slicing software such as ideaMaker. This software divides the model into layers that represent horizontal cross-sections of the finished print, and then adjusts the printing settings based on these variables. Some of these settings may include the use of support structures, layer height, and the choice of printing material. Once the digital file is sliced, it is sent to the 3D printer via wireless or cable connection.
Once the print is complete, it can be further refined or finished using post-processing techniques such as sanding, painting, or vapor smoothing. These steps can improve the surface quality, strength, and accuracy of the printed part. In addition, specialized tools like calipers and micrometers can be used to ensure that the printed product meets exacting specifications.
As the capabilities of 3D printing continue to evolve, it is becoming more common for manufacturers to use this technology for end-use products. For example, plastic and metal 3D printers are being utilized for medical devices such as hearing aids and prosthetic limbs that can be customized for each patient’s unique size and shape, resulting in better fit and performance.
However, the ability to customize end-use products using this technology is not without its challenges. In particular, some designs can be difficult to print due to limitations in the size of the build envelope, the mechanical properties of the printing materials, or other design considerations such as the need for supports. This can result in a delay in the delivery of the final product to customers, but it is important for manufacturers to work closely with their suppliers and partners to optimize the printing process for their particular applications.
Additive Manufacturing
Additive manufacturing uses 3D printing technology to turn digital CAD (computer-aided design) files into tangible three-dimensional objects. In its most basic form, the process involves layering various materials on top of each other to create the desired object. This technique allows for rapid prototyping and controlled on-demand manufacturing of patterns that can be used to manufacture the final product.
This approach to manufacturing has many benefits, including allowing engineers to quickly develop and test new parts in order to reduce the time it takes to go from the prototype stage to full production. It also allows manufacturers to better ensure that the final product will work as intended, reducing the risk of costly errors in the field.
Today’s advanced 3D printers are capable of printing a wide range of polymers, metals and ceramics. The most popular process is known as fused deposition modeling, or FDM, which uses spools of filament that are heated to a point where they can be extruded from a small nozzle in precise layers to build the desired part. The first layer forms a rough surface, and then the printed material hardens as it cools. As each additional layer is added, the part grows until it is fully formed and ready for use.
FDM is a relatively inexpensive method, which contributes to its popularity. However, it is not as accurate or durable as other processes, such as stereolithography (SLA) or selective laser sintering (SLS). SLA and SLS are both optical systems that use light to cure the material, producing the finished part.
Another popular 3D printing process is direct metal laser sintering (DMSL). This technology uses a laser or electron beam to melt and fuse metal powder together, creating solid parts. The resulting parts are robust and high-quality, which makes them ideal for industrial applications.
3D printing has become increasingly popular in the construction industry, with companies such as WinSun using large systems to print concrete components for building structures. This method provides faster construction times and more flexibility than traditional methods, as the component can be printed offsite, and assembled at the construction site.