Concrete Repair is the process of repairing deteriorated concrete by filling cracks, replacing damaged areas and making other structural repairs. Concrete repair methods must be economical, environmentally friendly and durable.
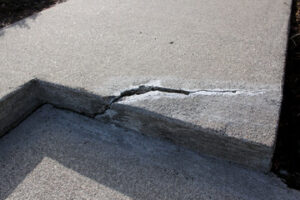
Compressive strength and abrasion resistance are important for most repair applications. Moisture vapor transmission, thermal expansion and bond are also key factors to consider. Visit Website to learn more.
Concrete crack stitching is a repair method that utilizes carbon fiber staples or stitches to stabilize the concrete structure. It is a great solution for structural cracks in foundation walls, retaining wall, swimming pools and poured concrete structures. It is more cost effective than epoxy grout filling and provides higher tensile strength.
Stitching is also used at longitudinal joints to prevent slab separation. Stitching is a rehabilitation technique that is done by drilling holes on either side of the joint and then inserting a carbon fiber stitch or staple in between to prevent movement. This is a much more durable and reliable solution than epoxy grout filling as it has higher tensile strength and the carbon fiber will not disintegrate or degrade over time.
Concrete can crack for a variety of reasons including temporary overload, changes in moisture conditions, poor soil compaction or subsidence. It can also be caused by unforeseen use or environmental factors such as changes in ground water levels and temperature. Cracks can range in size and appear at any time.
When it comes to concrete crack repair, it is important that the solution you choose has high tensile strength and the highest surface bonding area possible for long term performance. Stainless steel and steel composite materials like carbon fiber offer the highest strength to weight ratio in comparison to other metals. This is what makes it ideal for concrete crack stitching repairs as it offers a much stronger holding power than traditional metal staples or nails while minimizing the amount of movement in the concrete.
Drilling and Plugging
If your concrete structure has active cracks that are expanding and spreading, it is imperative that you take steps to prevent them from becoming worse. This can be done by using a method known as “crack stitching”. Crack stitching is a method of repairing active cracks that involves drilling holes and inserting metallic wires in the cracks to keep them from further widening. This technique can also help to re-establish tensile strength in concrete that has been compromised by structural cracks.
The routing and sealing method of repairing concrete cracks is another popular option. This involves using a router to enlarge the crack and then filling it with a sealant. This method is typically used for dormant cracks, but it can also be effective with active cracks if the right type of filler is chosen. Before applying the sealant, it is recommended that the cracks be cut into a V-shape and cleaned to remove any dirt or debris that could cause problems with the process.
In some cases, it may be necessary to use a more serious form of concrete repair such as concrete replacement. This is a method that should only be used by qualified engineers who are experienced in concrete construction.
Another way to repair concrete cracks is by using epoxy injections. This is a simple but effective method that can be used for cracks in expansion joints. However, it is important to note that this method will only be successful if the cracks are caused by water pressures or thermal expansion. It is not a suitable solution for cracks that are caused by settlement or other issues that require significant foundation work.
Routing and Sealing
The concrete crack repair process requires hard work, but choosing the right method can save time, money and energy in the long run. While this industry involves heavy machinery and tough labor, it also requires a lot of planning and critical thinking. The proper concrete crack repair methods are key in ensuring that projects are done right the first time.
Routing and sealing is a nonstructural crack repair technique that involves enlarging the crack (routing) then filling with a sealant or filler. This repair is used for both active and dormant cracks.
Prior to routing, field workers must first thoroughly clean the crack pavement area to remove all debris, leaves, sticks and other obstructive objects that may interfere with the routing process or inadvertently contaminate the routed channel. Routing is then completed with a large industrial asphalt pavement router that grinds a channel along the crack width.
This allows the low viscosity repair material to flow into narrow cracks via gravity. For smaller cracks, manufacturers have designed very small mixing nozzles that can be attached to hand-held dual-cartridge guns. These allow for very precise application of the repair materials into narrow cracks (photo 1).
Once the crack is routed, it can then be filled with a low-sag crack filler or sealant to stop water leaks and maintain surface integrity. This method is also often used to fill in expansion joints that have been compromised by traffic load, environmental factors and thermal movement. This is an effective method for repairing cracks in concrete surfaces, however, it is not a practical solution for structural repairs or stabilization of active and advancing fissures. For these applications, crack stitching is a more appropriate and effective repair method.
Epoxy Injection
Epoxy injection is a minimally-invasive method for repairing concrete structures. The process requires only small holes to be drilled for injection. The epoxy resin fills the cracks, voids, or delaminated areas and bonds the concrete surfaces together. This repair method is ideal for reducing costly downtime and structural replacements due to aging or structural overloading.
The surface to be repaired should be cleaned thoroughly to allow the paste-over epoxy to bond with sound concrete. Wire brushing is often sufficient in most cases, but in badly deteriorated concrete, high-pressure washing or V-grooving may be necessary. It is important to blow out any standing water from the crack with clean, oil-free compressed air to avoid contamination of the epoxy.
Once the area has been cleaned, surface ports are installed in the crack. This can be done using a manual or mechanical system. A surface port adhesive, such as Sealboss 4500 crack-sealer epoxy paste is applied on the face of the ports and the crack.
Injection begins by placing the epoxy into the lowest port in the crack, working upwards from there. Epoxy is usually injected until it appears to travel to the next port or the crack surface is completely filled. This allows the crack to be filled without wasting epoxy and helps provide uniform pressure throughout the crack.
Once the crack has been completely filled, the surface port adhesive is allowed to dry before injecting again. When a crack is leaking, it is a good idea to stop the injection and wipe down the injection port and paste-over. It is recommended to wait approximately 30 minutes for the paste-over to cure and begin to harden before reinjecting.
Urethane Sealant
When it comes to caulking and repairing gaps, there are many different types of sealants available. Two of the most popular options are silicone and polyurethane. Each has its own set of unique properties, so it’s important to choose the right type for your particular project.
Polyurethane sealants are tougher than silicones and are able to resist UV damage, making them an excellent choice for outdoor applications. They are also more flexible, which helps prevent water infiltration and slows the rate of cracking until a permanent repair can be made. Additionally, many urethane construction sealants are formulated using isocyanates or polyols derived from renewable resources, which reduces their environmental footprint.
To get the best results from your sealant, you will need to prepare your surface properly. First, remove any existing silicone sealant with a scraper or utility knife and clean the area to be repaired. Make sure the surface is free of dust, dirt, grease, rust, and other debris. Then, wipe it down with rubbing alcohol or isopropyl alcohol to ensure a good bond.
Next, you will need to select the proper concrete sealant for your project. A general purpose, non-sag, polyurethane sealant will work well for most projects, but there are also specific products designed to bond to concrete and other materials. For example, Loctite PL Concrete Non-Sag Sealant is perfect for repairing concrete walls, foundations, and brick or stone walls. This product is formulated to bond to concrete, brick, stucco, metal, wood, vinyl, and fiberglass and resists deterioration caused by weather or movement. It also requires no primer for concrete applications and dries to a dark gray color. This allows you to easily match the color of your existing concrete surfaces.