Bakersfield Concrete Contractor Services should have a portfolio of past projects. They should also be able to answer questions about their work and give references.
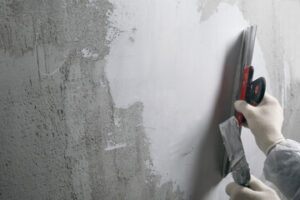
A concrete contractor should be familiar with the permits required for commercial projects. They should be able to obtain these permits quickly and efficiently.
Even the smallest concrete contractors have access to technology that was unimaginable a few years ago. From field service management tools to collaboration software, these technologies streamline business processes and allow concrete contractors to deliver faster and more accurately.
Concrete contractors are specialized professionals who offer a range of services related to the construction and repair of concrete structures for commercial properties. They are highly trained in concrete technology and can handle a wide variety of projects, from building new foundations and floors to repairing and maintaining existing concrete structures. They also have the experience necessary to work on larger-scale construction projects, such as those found in office buildings and shopping malls.
Before choosing a concrete contractor, it is important to check their qualifications. A reputable company should be able to provide you with references from past customers and should have the proper licenses and insurance required for the type of work you need done. They should also be able to provide you with an estimate for the project and answer any questions you may have.
One of the most important aspects of a good concrete contractor is their ability to meet deadlines and budgets. They should have a team of dedicated workers and the right equipment to ensure that the job is completed on time and within budget. In addition, they should be able to consult with engineers and architects to ensure that their concrete work is in line with the design and structural requirements for the project.
A quality concrete contractor will be able to provide a variety of services to their clients, including completing a full excavation, preparing the site for concrete pouring, and finishing the concrete after it has been poured. They will also be able to assist with the development of the design for the concrete structure and can recommend materials and finishing options that will enhance the aesthetic appeal of the finished product.
Finally, a quality concrete contractor will be able to offer a warranty on their work and materials. This is important because concrete can be very finicky and can crack or deteriorate over time. It is essential to find a contractor who offers a warranty that will last for several years.
To become a concrete contractor, it is recommended that you attend construction school and take courses in business management and estimating. These skills are essential if you want to run your own concrete contracting company. You can also learn the skills by working as a laborer on a concrete crew or joining a concrete mason union apprenticeship program, which usually provides classroom and hands-on training.
Reputation
Concrete is a vital building material and is used in the construction of many different types of facilities. This is why it is important to find a reputable concrete contractor. Whether you are looking for a commercial or residential concrete contractor, it is crucial to check their reputation and the quality of their work. You can do this by asking for references or searching online reviews. It is also a good idea to ask for quotes from several contractors and compare prices before making a decision.
A reputable commercial concrete contractor should have years of experience working on different types of projects. They should also be licensed and insured in order to meet local regulations. Additionally, they should be able to provide you with examples of their past work. They should also be able to answer your questions about their pricing structure and any other details related to the project you are considering.
It is also a good idea to get referrals from friends and family members. They may have used a concrete contractor in the past and can tell you about their experiences. It is also a good idea to search for online reviews on websites like Yelp or Google. These reviews can give you an idea about the contractor’s quality of work and customer service.
A professional concrete contractor will know how to work closely with architects and engineers throughout the process. They will ensure that the concrete work meets building codes and other structural requirements. They will also help to select appropriate construction techniques and materials. In addition, they will make sure that the concrete is built to withstand the load and conditions of the site.
A reputable concrete contractor will have a strong track record of providing exceptional results on time and within budget. In addition, they will have a solid understanding of industry best practices and will be able to advise you on the most effective solutions for your specific project. Additionally, a good commercial concrete contractor should be able to provide you with references from previous clients and proof of insurance.
Insurance
When you work in the concrete business, it’s important to have the right insurance coverage. This ensures that you and your employees are protected in the event of an accident or a claim. It also shows clients and general contractors that you’re a responsible contractor who takes care of your workers and their property. The type of insurance coverage you need varies depending on the size of your business and the risks associated with it.
General liability insurance, or GL, is an essential part of any concrete contractor’s policy. It covers the legal and financial costs of accidents or injuries that are alleged to have occurred while you are working on a project. The policy also pays for any expenses related to defending your company in the case of a lawsuit.
Commercial property insurance is another must-have for concrete and cement contracting companies. It covers losses to your business’s physical structure and any machinery or equipment stored there. Common perils include fire, flood, windstorms, and vandalism. Having this insurance will help you recover from these types of disasters quickly and without a lot of expense.
Another type of concrete contractor insurance is worker’s compensation. This is required by law in most states, and it protects you in the event of an employee’s injury while working on a project. It also covers lost wages and medical treatment. Many clients and general contractors require that you have this type of insurance before letting you work on their projects.
If you have a reputation for delivering high-quality services, you may be able to negotiate lower rates for your concrete contractor services. Some insurers offer discounts based on the length of time you’ve been in business and your claims history. You can also reduce your premium by implementing safety measures in your office and on the job site.
There are several factors that can affect the cost of concrete contractor insurance. The number of employees, the amount of damage to property, and the location of your business are just a few examples. Those in higher-risk industries, like construction, typically pay more for their business insurance. The cost of your insurance can also be affected by your credit rating.
Pricing
Concrete Contractor Services can range in price, depending on the size and complexity of the project. However, it is important to get quotes from multiple contractors before making a decision. This will allow you to compare prices and services, and choose a company that fits your budget. It is also a good idea to check references and reviews. Many contractors will post these online, so you can read about others’ experiences with them.
Concrete is a complex material that requires expertise and experience to install properly. Choosing the right contractor can save you time and money, as well as ensure that your concrete project is completed on time and within budget. A reputable concrete contractor will have an extensive knowledge of different types of concrete and their best applications, and will be able to recommend the right mixtures for your specific needs.
Commercial concrete contractors also have a thorough understanding of local building codes and regulations, and are able to work closely with architects and engineers to ensure that their concrete work integrates seamlessly with the overall design and structural requirements of the project. They are also able to advise on site preparation and other necessary steps that may be required to ensure that the concrete can withstand the intended loads and conditions.
It is also important to note that the price of a concrete project will depend on the amount of labor and equipment involved. A commercial concrete contractor typically has a team of experienced workers and a fleet of specialized equipment, which helps them to work efficiently and keep projects on schedule. In addition, a reputable concrete contractor will provide detailed estimates that will include all of the relevant costs for the project.
Some contractors will charge extra for site prep, particularly if the area is hard to access. This is because the soil beneath the concrete is critical to its structural integrity, and if it is not properly prepared, the slab will be more likely to crack or sink over time.
While being a concrete contractor is a highly skilled job, becoming a successful subcontracting business owner takes more than just knowledge of the trade. To thrive, you need to be a master of managing your finances, hiring employees, and streamlining project management. To help you do so, a construction resource management tool like eSUB can make all the difference.